微纳米加工及应用
绪论
微纳加工的特点:
- 微纳加工是在衬底表面通过薄膜材料沉积和图形化的方法实现的,平面工艺一般只能形成二维平面结构,准三维结构通过多层二维叠加形成
- 微细结构一般由曝光成像的方法形成,而不是加工工具与材料的直接相互作用
- 复杂微纳米系统是在平面加工过程中形成的,是一个逐层进行且不可逆过程
微纳加工的基本过程:薄膜沉积→图形成像→图形转移【课后复习题】
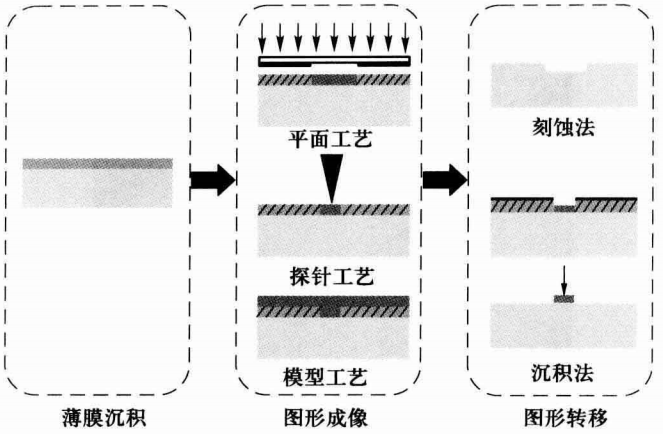
图形成像:平面工艺;探针工艺;模型工艺
图形转移:刻蚀法;沉积法
集成电路工艺主要包括4个主要方面:薄膜沉积;制图;掺杂;热处理
广义的光刻包括:光学曝光;电子束曝光;离子束曝光和X射线曝光,激光直写
强酸中毒的应急处理方法:
①沾着皮肤时,用大量水冲洗15分钟 (稀释减少中和热伤害),再用碳酸氢钠之类稀碱液或肥皂液进行洗涤
②当沾着草酸时,不宜使用碳酸氢钠,可以用镁盐和钙盐中和
误食氢氟酸喝大量的水或牛奶,不能催吐
强碱中毒的应急处理方法:
①沾着皮肤时,尽快用水冲洗至皮肤不滑为止,接着用经水稀释的醋酸或柠檬汁等进行中和;
②沾着生石灰时,则用油之类东西,先除去生石灰
呼吸道吸入刺激性或有毒气体应急处理办法:
①吸入氯气、氯化氢气体时,可吸入少量酒精和乙醚的混合蒸气使之解毒
②吸入硫化氢或一氧化碳气体而感不适时,应立即到室外呼吸新鲜空气
微纳米加工和传统机械加工有什么不同?【课后复习题】
属性 | 微纳米加工 | 传统机械加工 |
---|---|---|
加工尺度 | 微米/纳米级(10⁻⁶至10⁻⁹米) | 毫米级及以上 |
精度 | 公差可达到纳米级别 | 公差在微米级别 |
加工方法 | 光刻、电子束刻蚀、聚焦离子束刻蚀、纳米压印等 | 切削、研磨、钻孔等物理加工 |
设备与环境 | 专业设备,高洁净环境(超净室) | 通用机械设备,一般环境 |
材料选择 | 硅等半导体和功能材料 | 金属、塑料、木材等宏观材料 |
成本与效率 | 产量低、生产成本高 | 产量高、生产成本低 |
应用领域 | 半导体制造、MEMS传感器、纳米技术 | 机械设备、汽车制造、航空航天 |
在超净室工作有哪些日常行为规范?【课后复习题】
- 按顺序穿戴洁净服、帽子、口罩、手套,通过风淋室
- 规范操作,定期参加洁净室操作规程培训
- 及时清理垃圾,定期清洁设备和工作区
课后复习题:
- 微纳米加工的基本过程是什么?
- 微纳米加工和传统机械加工有什么不同?
- 在超净室工作有哪些日常行为规范?
光学曝光技术
光学曝光方式与原理
光学曝光的方式:掩模对准式曝光与投影式曝光【课后复习题】
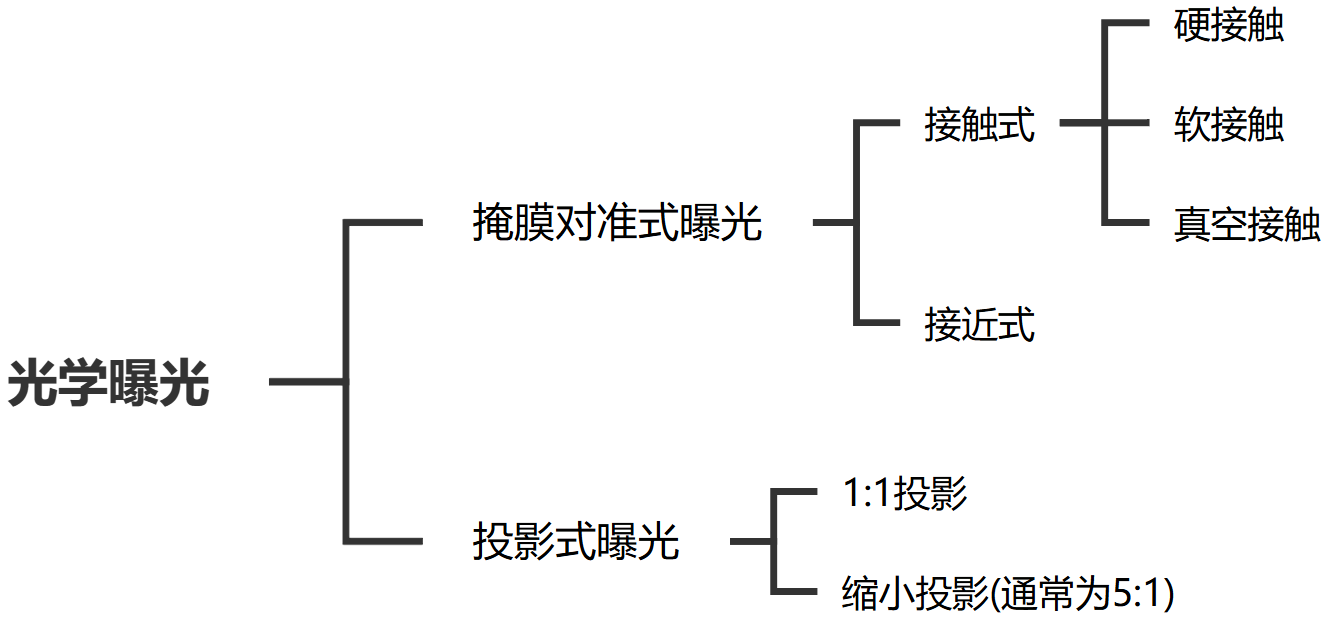
真空接触:使经过多道工序加工而翘曲的基片恢复平整,从而保证曝光时投射到胶表面的光强分布均匀;使掩膜与胶表面接触更加严密,从而获得更高的分辨率
光学曝光方式各有什么优缺点?【课后复习题】
优点 | 缺点 | |
---|---|---|
掩膜对准式曝光 | 曝光分辨率较高; 工艺简单且设备成本较低; |
光学分辨率有限,掩膜和衬底之间可能接触; 曝光过程较慢,不适合大规模生产; |
投影式曝光 | 曝光分辨率最高(高NA,短波长); 掩膜不接触衬底; 图像可缩放,适合大规模生产; |
设备复杂且昂贵,需要精密的光学系统和高效的光源; 掩膜图案通常需要缩放,掩膜制作更加复杂 |
工业主要采用投影式曝光,它的图像质量完全取决于光学成像系统,与掩模-基片之间的距离无关
光学曝光工序
光学曝光工序有哪些?【课后复习题】
基片表面处理、涂敷光刻胶、前烘、曝光、后烘、显影、清除残胶、坚膜、图形转移、去胶等
前烘的目的:去除胶膜中残存的溶剂,使胶膜干燥,以增强胶膜与基片的粘附性和胶膜的耐磨性
后烘的目的:部分消除驻波造成的影响,但是也会导致胶中光活性物质横向扩散,影响胶的图形质量
光线照射到光刻胶与基片界面上会产生部分反射,反射光会使掩模不透光区下边的光刻胶进行曝光,反射光与入射光叠加会形成驻波,驻波会造成光刻胶边缘曝光结果出现螺纹状
如果涂胶前在基片上先涂覆一层抗反射层或涂胶后在胶表面施加抗反射剂则可以有效防止驻波效应
图形转移:通常通过 干法刻蚀 和 湿法刻蚀
光刻胶的评价指标有哪些?【课后复习题】
灵敏度、对比度、抗刻蚀比、分辨能力、曝光宽容度、工艺宽容度、热流动性、膨胀效应、粘度、保质期限
灵敏度是衡量曝光速度的指标,灵敏度越高,所需要的曝光剂量越小
对比度越高,曝光的线条边缘越陡
抗刻蚀比是衡量在刻蚀过程中保护下层材料的能力
分辨能力影响最小线宽
正胶和负胶的区别:【课后复习题】
曝光反应 | 显影结果 | 图案关系 | 灵敏度 | 对比度 | 分辨率 | 显影液 | 残胶现象 | 成本 | |
---|---|---|---|---|---|---|---|---|---|
正胶 | 曝光后可溶解 | 未曝光区域保留 | 与掩膜一致 | 较低 | 高 | 高 | 水溶性 | 少 | 较高 |
负胶 | 曝光后不可溶解 | 未曝光区域被去除 | 与掩膜相反 | 高 | 低 | 较低 | 有机溶剂(污染环境) | 较普遍 | 较低 |
课后复习题:
- 光学曝光的方式有哪些?各有什么优缺点?
- 光学曝光的工序一般有哪些?
- 光刻胶的性能指标有哪些?正胶和负胶有什么区别?
光学曝光的分辨率
特征尺寸(CD):掩膜设计的最小图形尺寸
最小线宽:$l_{CD}=\sqrt {\lambda z}$,反映了制造工艺的分辨能力
$\lambda $ 是曝光光源的波长,$z$ 是掩模版与基片间的间隙距离
数值孔径的定义: 【课后复习题】
平行光通过透镜后聚焦成一直径有限的光点时,最外光线与光轴间夹角$\theta $的正弦值与透镜和基片之间介质的折射率$n$的乘积
NA对光学曝光分辨率和焦深有什么影响?【课后复习题】
数值孔径越大,分辨率越高,焦深越小
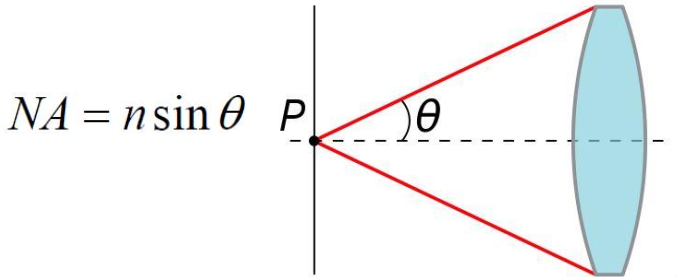
光学分辨率的定义: 【课后复习题】
能精确转移到晶片表面光刻胶图案的最小特征尺寸
$$
R=k_{1} \frac{\lambda}{N A}
$$
分辨率可以通过减小曝光波长和增加数值孔径来实现
焦深的定义: 【课后复习题】
指能够满足光刻分辨率与特征尺寸均匀性的基片最大离焦范围
$$
D=k_{2} \frac{\lambda}{(N A)^{2}}
$$
$k_{1} ,k_{2} $ 为与工艺相关的参数,$k_1$的理论极限是0.25
焦深可以通过增大曝光波长和减小数值孔径实现
单纯追求分辨率会使得焦深大大降低,分辨率只有在一定焦深范围才有意义
焦深太小,掩模成像只在很小的高度起伏范围内才能保证聚焦,超过这一范围就会散焦
有哪些短波曝光技术? 【课后复习题】
深紫外光刻(DUV)、极紫外光刻(EUV)、X射线曝光技术
短波曝光技术面临的问题: 【课后复习题】
技术 | 波长范围 | 主要挑战 |
---|---|---|
DUV | 193 nm、248 nm | 分辨率受限,面临光波长和数值孔径的物理限制; 为实现更小特征尺寸,需要通过多重曝光、多重图案化等方法提高分辨率,工艺复杂度高; |
EUV | 13.5 nm | 光源输出功率较低且难提高,导致曝光效率低,生产速率缓慢; 光刻胶材料需要更高的灵敏度和分辨率; |
X 射线 | 0.1–10 nm | 光源技术尚不成熟,难以实现高功率; 掩模制造困难,需要有X射线的高透明性,且掩膜图样精细度高; 分辨率受限,难以获得与波长相对应的曝光分辨率 ; |
193nm波长的深紫外光刻使用水作为浸没液体
什么是大数值孔径和浸没式曝光技术?为什么要发展他们?【课后复习题】
大数值孔径技术:通过增加光刻机镜头的数值孔径来提高分辨率
浸没式曝光技术:在光刻过程中,将镜头与基片之间的空气替换为高折射率的液体(通常是水),增加光学系统中的折射率来提高数值孔径 NA,从而提升分辨率
发展它们是为了突破传统光刻的物理限制
课后复习题:
光学曝光的分辨率和焦深是什么意思?他们由什么决定?
有哪些短波曝光技术?他们都面临什么样的问题?
什么是数值孔径?它对光学曝光分辨率和焦深有什么影响?
什么是大数值孔径和浸没式曝光技术?为什么要发展他们?
分辨率增强技术
分为对光学系统的改进和对掩膜版的改进
针对曝光光学系统和光刻掩膜,有哪些分辨率增强技术? 【课后复习题】
光学曝光工艺环节 | 分辨率增强技术 |
---|---|
照明光学系统 | 离轴照明技术 |
成像光学系统 | 空间滤波技术 |
光学掩模 | 移相掩模技术,光学邻近效应校正技术 |
离轴照明技术:
传统曝光系统的光源是通过一个中心圆孔进入聚光透镜系统
离轴照明技术采用倾斜照明方式,照明光束以偏离主光轴方向$\theta /2$入射,用从掩模透过的零级光和其中一个一级衍射光成像,让包含主要结构信息的低频分量和部分包含精细特征的高频分量都进人系统,因而可以提高分辨率,改善像质;由于是双光束对称成像,还可改善焦深
传统照明系统 | 离轴照明系统 |
---|---|
$\begin{aligned}R_{\text {传统 out }- \text { off }}=\frac{\lambda}{2 N A(1+\sigma)} \end{aligned}$ | $\begin{aligned}R_{\text {离轴 out }- \text { off }}=\frac{\lambda}{2 N A(1+\sigma)+2 \theta_{i}} \end{aligned}$ |
$\sigma $ 为曝光系统的部分相干因子,$\theta_{i} $ 为离轴照明光束的入射角;与传统照明相比,离轴照明提高了分辨率
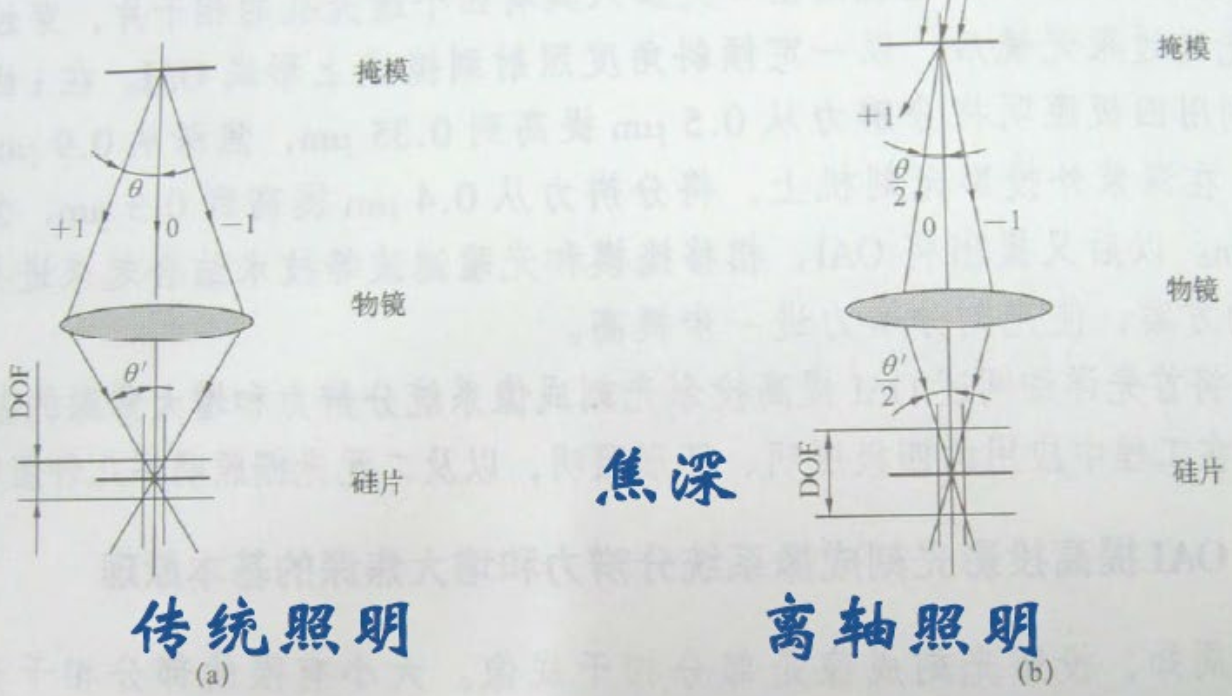
空间滤波技术:
在透镜的光阑平面上通过加滤光片,滤波片的不同环区对入射光有不同的透射率和相位差,从而部分遏制低频分量,突出高频分量,使得图像清晰度增加
移相掩膜技术:
通过移相掩模使两个紧邻清晰区域各自引入0°和180°的相位差,改变了电场的符号,减少了硅片上两个光孔之间黑暗区域的光强,以此来改进图像对比度,从而导致了更好的分辨率和焦深
什么是光学临近效应?【课后复习题】
光学临近效应是指在光刻过程中,由于光通过掩膜图案时发生的干涉和衍射,导致实际在衬底上形成的图形与设计图形存在偏差,这种效应会引起线宽变化、图形畸变和位置误差,比如方角图形变成圆角,或者线端变短,影响半导体器件的精度和性能。
光学邻近效应的校正:【课后复习题】
线条偏置法(形状调整法):对原设计增加或减少部分图形
加衬线法:通过在掩模上添加亚分辨辅助线条,使孤立的空间像能和密集线条的空间像具有相同的线宽
灰度掩膜法:调整掩模图形的局部透光率;(类似剂量校正)
传统掩模上只有透光区与不透光区,而灰度掩模的透光率则是以灰度等级来表示,实现灰度的方法是改变掩模的透光点密度,一种是改变透光点的大小,一种是改变透光点的数目,也可以二者相结合
可以突破光学曝光分辨率的理论极限的方法【课后复习题】
在没有任何技术优化的情况下,$k_1$的理论下限为0.61;使用了分辨率增强技术后接近于理论下限0.25;
多重曝光和加工技术是唯一可以进一步突破$k_1$理论极限的技术;
多重曝光:设计子图案掩膜,多次曝光;
多重加工:曝光刻蚀后再曝光再刻蚀;
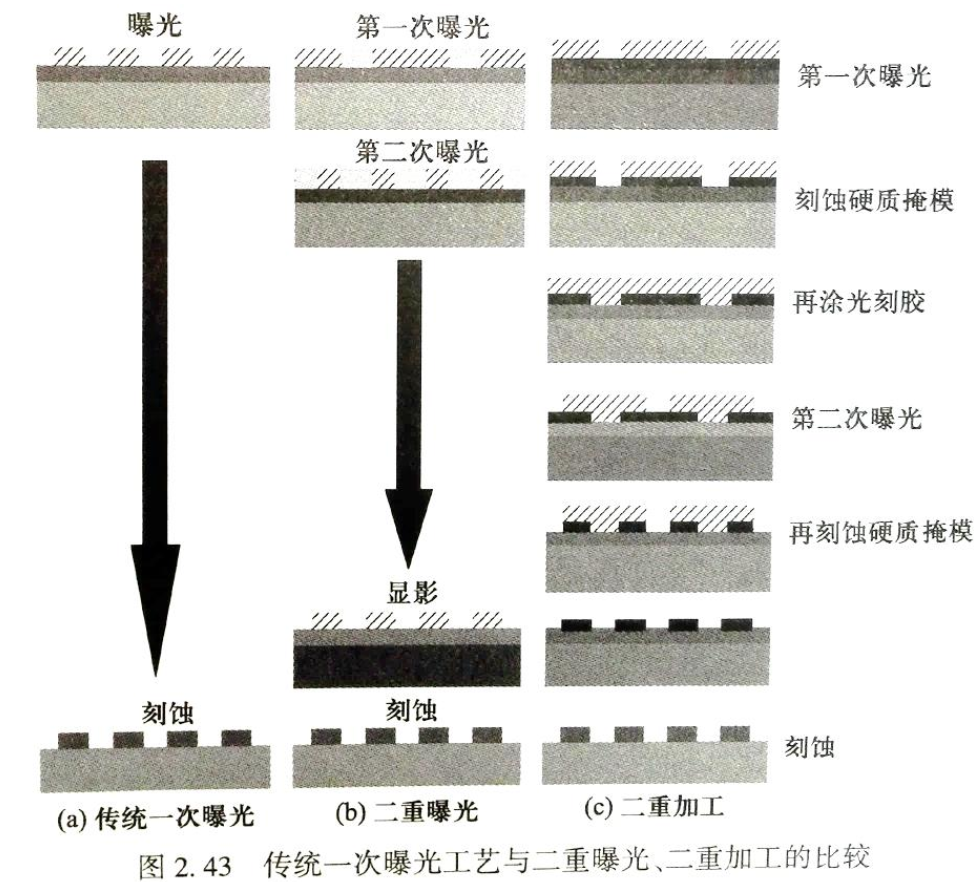
课后复习题:
- 针对曝光光学系统和光刻掩膜,有哪些分辨率增强技术?
- 什么是光学临近效应?可以通过什么方法进行校准?
- 有什么方法可以突破光学曝光分辨率的理论极限?具体是怎么实现的?
电子束曝光技术(EBL)
电子束曝光系统
电子束曝光(electron beam lithography):利用某些高分子聚合物对电子敏感而形成曝光图形
光学曝光分辨率:
$$
R=k_1\frac{\lambda }{NA}
$$
受光波长的限制:G线(436nm)→I线(365nm)→DUV(248,193nm)→EUV(13nm)
根据波粒二象性,电子波长
$$
\lambda_e=\frac{1.226}{\sqrt V} \text{nm}
$$
电子光学像差:决定最小束斑直径
一般像差:其中以球差和色差为主
偏转像差: 电子束离轴后形成的像差,如像散和场曲
空间电荷效应像差: 空间电荷排斥效应会使电子束直径增大,破坏聚焦(小束斑需要小束流)
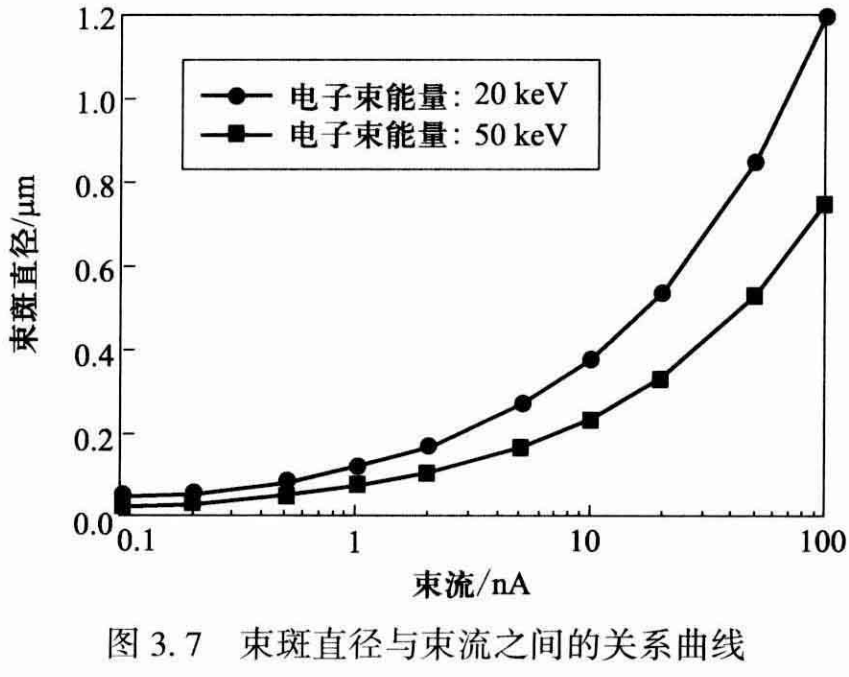
电子束抗蚀剂
两种分类
正型 | 负型 |
---|---|
显影后曝光区域溶解 | 显影后未曝光区域溶解 |
PMMA,ZEP-520 | HSQ |
PMMA过曝光时可从正胶转变为负胶特性,但抗刻蚀能力差(ZEP-520抗刻蚀能力强)
传统型 | 化学放大型 |
---|---|
抗蚀剂中聚合物分解在曝光过程中完成 | 抗蚀剂中聚合物分解在后烘过程中完成 |
和光刻胶的正负性质相同
传统型:抗蚀剂中的聚合物分解或链接是在曝光过程中完成
常见高分辨率电子束抗蚀剂:
化学放大型优点:具有高灵敏度,兼有高分辨率;高对比度;高刻蚀比
化学放大型缺点:后烘工艺条件要求高;存在延迟效应和表面污染
实际曝光剂量的决定因素:
因素 | 剂量变化 |
---|---|
电子束能量 ↑ | ↑ 曝光主要靠低能量电子 |
抗蚀剂厚度 ↑ | ↓ 抗蚀剂越薄,其中电子能量沉积越少 |
图形密度 ↑ | ↓ 电子散射互相影响 |
衬底材料密度 ↑ | ↓ 高密度衬底会产生更多背散射电子 |
and 抗蚀剂工艺条件:后烘温度、显影液温度和强度等
多层胶工艺:从下到上灵敏度逐渐降低,形成undercut结构
影响电子束曝光分辨率的因素有哪些?【课后复习题】
主要受电子像差和电子散射的影响,高分辨率需要小束斑,影响因素如下:
影响因素 | |
---|---|
加速电压(电子束能量) | 加速电压越大,电子能量高,可以减少散射角,获得更小的束斑与更高分辨率,但影响曝光深度,加速电压需适中 |
束流大小 | 束流强度决定单位时间照射到样品的电子数量,小束流空间电荷效应小,可以获得小束斑 |
抗蚀剂厚度 | 抗蚀剂越薄,电子在内部散射越少,有助于提高分辨率 |
抗蚀剂灵敏度 | 低灵敏度抗蚀剂具有更高的分辨率和对比度 |
图形密度 | 图形密度低,邻近效应小 |
衬底密度和导电性 | 衬底密度越低背散射越少,导电性强可以降低电荷积累效应 |
如何抑制电子束与抗蚀剂作用范围的扩展? 【课后复习题】
即减少电子散射范围
- 增大电子束的能量
- 降低束流大小
- 控制曝光剂量;
- 采用更薄的抗蚀剂层;
- 使用高分辨率抗蚀剂(快速反应,减少累计散射)
针对高灵敏度和低灵敏度的问题举例:
- PMMA(聚甲基丙烯酸甲酯):作为一种典型的低灵敏度抗蚀剂,PMMA在高剂量下表现出优异的分辨率,广泛应用于纳米级图形的制备。然而,其高剂量需求也可能导致较大的邻近效
应,需要通过优化曝光和显影工艺来控制 - ZEP和其他高灵敏度抗蚀剂:这些抗蚀剂在较低的电子剂量下即可实现有效曝光,适用于需要快速曝光和抑制邻近效应的场景,但在分辨率上可能不及PMMA
电子束曝光成像质量
电子束在抗蚀剂和基底材料中的散射:
散射深度 | 散射范围 | |
---|---|---|
电子能量 ↑ | ↑ | ↑ |
衬底密度 ↑ | ↓ | ↓ |
衬底密度越高导致背散射电子增加, 背散射造成的邻近效应可波及几个微米,造成密集图形变形失真
光学曝光邻近效应和电子束曝光邻近效应导致的原因有何不同?【课后复习题】
光学曝光:干涉和衍射;
电子束曝光:电子散射;
如何校准电子束曝光的临近效应?【课后复习题】
图形校正:对掩膜图形进行调整,避免过度曝光
剂量校正:根据邻近效应模型,调整每个图案的曝光剂量,消除邻近区域的过度曝光
背景曝光:第一次对曝光图形进行正常曝光,第二次将所有没有图形的地方以散焦的电子束和低剂量进行曝光,目的是补偿能量
课后复习题:
- 影响电子束曝光分辨率的因素有哪些?
- 如何抑制电子束与抗蚀剂作用范围的扩展?
- 导致光学曝光临近效应和电子束曝光临近效应导致的原因有何不同?如何校准电子束曝光的临近效应?
聚焦离子束曝光技术(FIB)
聚焦离子束(Focused Ion beam)成为一种用途广泛的微纳加工工具,因为具备4个特点/功能:
(1) 材料表面加工;(2)注入掺杂,材料改性;(3)材料沉积;(4)高分辨能力
液态金属离子源(LMIS):利用液态金属在强电场下形成场致离子发射离子源(液态金属Ga)
离子在固体中会经历一系列散射,在散射中不断损失能量,最后停止并留在固体中
离子束和材料的相互作用与电子束和材料的相互作用有何不同?【课后复习题】
最主要区别在于粒子的质量和电荷,离子束具有较大质量和多重电荷,电子束质量轻、电荷单一
离子束:通过直接的物理溅射和材料表面原子碰撞来移除材料,表面损伤较大
电子束:通过电子与材料的电荷相互作用来产生光刻效应,有电子散射,表面损伤较小
比较离子束曝光技术与电子束曝光技术【课后复习题】
特性 | 离子束曝光(FIB) | 电子束曝光(EBL) |
---|---|---|
工作原理 | 使用聚焦离子束直接轰击,使其发生化学或物理反应 | 电子与抗蚀剂相互作用引发化学反应 |
加工方式 | 既可以进行曝光,也可进行直接加工图形 | 通过抗蚀剂间接加工,需要后续刻蚀工艺 |
相互作用深度 | 离子相互作用集中在材料表面(几纳米至几十纳米) | 电子在材料中穿透较深(几十纳米至几微米) |
分辨率 | 分辨率更高,适用于亚纳米级加工 | 分辨率高,适用于纳米级图案加工 |
曝光速度 | 曝光速度较慢,适合小面积高精度加工 | 曝光速度较快,适合大面积图案加工 |
应用场景 | 高精度表面修饰、纳米结构直接雕刻 | 高分辨率曝光、纳米图案加工 |
离子束加工的原理有哪些?【课后复习题】
离子溅射:入射离子将能量传给靶材原子,使其获得足够能量而逃逸出固体表面的现象,是离子束加工的最主要功能
离子束辅助沉积:吸附在靶材表面的非活性气体分子在离子束的轰击下发生分解,生成固态物质沉积在材料表面
离子束加工技术的应用有哪些?【课后复习题】
审查与修改集成电路芯片;修复光刻掩模缺陷 ;制作透射电镜样品;多用途微切割工具
什么是离子束注入技术?【课后复习题】
离子束注入技术是一种利用高能离子束将离子注入材料表面的物理技术,控制离子掺杂和材料改性
课后复习题:
- 离子束和材料的相互作用与电子束和材料的相互作用有何不同?
- 离子束加工的原理有哪些?
- 离子束加工技术有哪些应用?
- 比较离子束曝光技术与电子束曝光技术
- 什么是离子束注入技术?
扫描探针加工技术
扫描探针加工技术的优缺点:
- 优点:简单易行
- 缺点:加工精度有限;加工深度有限;加工速度极低;加工面积极小
扫描探针显微镜:
STM:扫描隧道显微镜
SFM:扫描力显微镜
NSOM:扫描近场光学显微镜
扫描隧道显微镜(STM)
STM的成像原理:【课后复习题】
当探针与样品表面距离足够近时,电子发生隧穿效应,产生一个非常小的电流,距离越近,隧道电流越大;
STM通过精确的反馈系统控制探针的高度,使得隧道电流保持恒定,STM可以记录探针的位移,这个位移的变化反映了样品表面的高度变化,形成样品表面的高度图像。
原子力显微镜(AFM)
AFM的成像原理:【课后复习题】
将对微弱力极敏感的微悬臂一端固定,另一端有一个非常尖锐的探针(通常由硅或氮化硅制成)
当探针接近样品表面时,探针尖端和样品表面的原子之间会产生不同的相互作用力,如范德华力、电磁力等,扫描时控制力的恒定,通过使用光学系统(通常是激光反射装置)来检测悬臂的位移,从而获得样品的表面形貌信息。
在AFM中探针与样品原子之间有两种类型相互作用力
- 短程力:在针尖与样品表面接触时相互作用力主要是短程的原子间斥力,如泡利斥力和离子斥力、磨擦力等
- 长程力:当针尖离开样品表面10nm~100nm或更大时,如象磁力、静电力和范德瓦尔斯力等
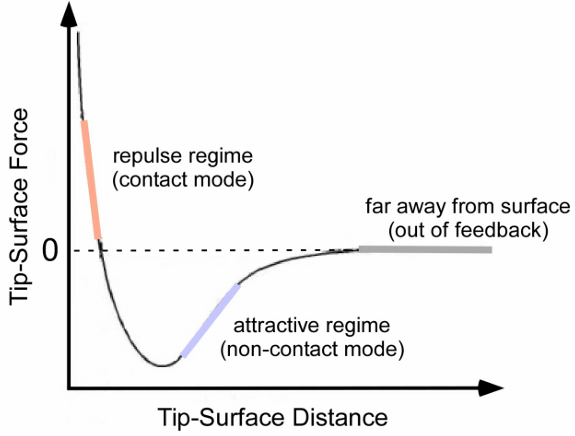
短程力的作用范围在0.1mm以下,把工作在这种模式下的AFM称为接触式AFM
最主要用的是Tapping mode
AFM的类型 | 优点 | 缺点 |
---|---|---|
接触式AFM (Contact Mode) | 高扫描速度; 高分辨率(原子分辨率); 可以扫描表面极端变化的样本; |
横向力、摩擦力可能会扭曲图像中的特征; 探针与样品表面直接接触,可能导致样品的损坏; 接触导致探针磨损,进而影响成像精度和分辨率 |
轻敲式AFM(Tapping mode) | 横向分辨率更高(1~5nm); 几乎消除了侧向力; 减少了样品损伤; |
扫描速度比接触式AFM较慢 |
非接触式AFM(Non-contact Mode) | 样品表面不受力,避免样品损伤 | 横向分辨率较低,受针尖-样品分离影响; 扫描速度比接触与轻敲慢,以避免针尖被卡住; 只适用于疏水性极强的样品; |
分辨率的影响因素:
- 针尖半径:探针尖端的半径越小,分辨率越高;
- 针尖侧面角:决定最高表面比率特征的探测能力
- 成像模式:接触、轻敲、非接触
扫描近场光学显微镜(SNOM)
SNOM与STM或AFM的基本区别是将固体扫描探针换成一个扫描光源,光源扫描由光纤探针实现
近场光学成像分辨率与入射光波长无关, 只与光探针的大小(数值孔径)有关
优点:突破衍射极限;非破坏性分析;多维信号获取
SNOM通常有两种工作模式:
- 透射模式:光通过样品,然后被探针采集,这种模式适用于透明样品
- 反射模式:光反射回样品表面并被探针捕获,适用于不透明样品
扫描探针加工技术
抗蚀剂曝光加工(一般不咋用)
包括STM曝光、SNOM曝光
STM曝光的一些问题:
问题 | 具体解释 |
---|---|
抗蚀剂层必须很薄 | 由于探针的针尖必须非常靠近作为阳极的衬底材料表面才能产生足够高的场致发射电流,用STM曝光的抗蚀剂一般不超过50nm厚 |
曝光分辨率≤成像分辨率 | 相比于电子束曝光利用聚焦电子束,STM针尖发射的电子束是发散束,发散程度取决于施加的偏压和探针与抗蚀剂表面的距离 |
曝光所需剂量大 | STM曝光的特点是低能电子束曝光,曝光同样尺寸图形时,STM曝光的剂量是传统曝光的30倍 |
局部氧化加工
STM或AFM针尖处的强电场使得空气中的水分子在针尖附近被电离成离子态,然后将衬底材料氧化,扫描针尖形成加工图形
反应影响因素:偏压、探针在某一点的停留时间,环境空气湿度等

环境湿度对局部氧化层起着重要作用:
- 湿度越大,供给局部氧化的水分子越多,氧化越快;
- 湿度会影响针尖局部电场的分布;
- 湿度较大时,会在针尖和样品之间形成一层水膜,使局部电场发散和局部氧化范围增加,造成氧化线条变宽
STM不能反馈氧化层的变化,氧化层的生长导致隧道电流和针尖表面距离的减小,但STM反馈系统会增大探针偏压,且不会同步抬起探针,易导致探针受损
AFM的偏压独立于探针高度的反馈控制系统,可以很好地适应氧化物的生长;且氧化层的厚度可以原位实时监测
AFM更适合扫描探针局部氧化加工
添加式纳米加工
包括:场致沉积加工、蘸笔纳米探针加工
抽减式纳米加工
包括:电化学刻蚀加工、场致分解加工、热力压痕加工、机械划痕加工
扫描探针加工技术有哪些方式?【课后复习题】
抗蚀剂曝光加工;局部氧化加工;添加式纳米加工;抽减式纳米加工;高产出率扫描探针加工
课后复习题:
- STM和AFM的成像原理是什么?
- 扫描探针加工技术有哪些方式?
复制加工技术
纳米压印是一种全新的纳米图形复制技术
纳米压印技术的特点是什么?【课后复习题】
超高分辨率、高产量、低成本
高分辨率:没有光学曝光中的衍射现象和电子束曝光中的散射现象
高产量:可以像光学曝光那样并行处理,同时制作成百上千个器件
低成本:不像光学曝光机那样需要复杂的光学系统或像电子東曝光机那样需要复杂的电磁聚焦系统
热压纳米压印技术
纳米压印过程包括的主要步骤: 【课后复习题】
- 涂覆聚合物涂层(如PMMA);【PMMA是最早用来作为压印层的聚合物】
- (在一定温度下)模具对准与压印;
- 聚合物固化,然后从基底上移除模具;
- 反应离子刻蚀去残胶,后续可进行图形转移
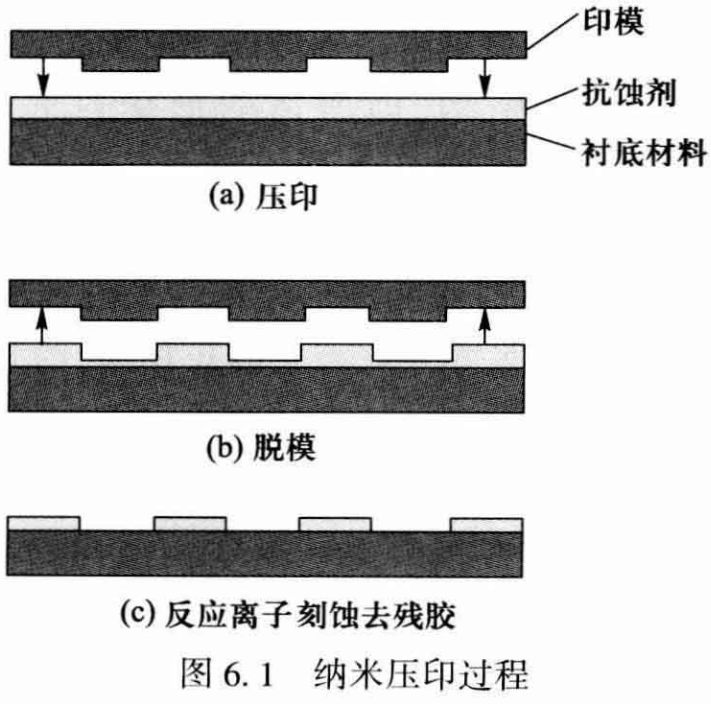
实现高质量纳米压印取决于印模、压印涂层材料、脱模技术、对准精度
热压纳米压印最适合于制作均匀的、小尺寸的、阵列式的图形
印模 | 压印材料 | |
---|---|---|
要求 | 印模和印模图形必须是硬质材料,如硅、氧化硅、氮化硅、金属等; 印模图形由电子束/光学曝光技术/激光直写加工; 最经久耐用的印模材料是金属镍 |
较低的玻璃化转变温度$T_g$,降低压印温度; 较低的粘塑性,保证聚合物材料的流动性和印模空腔的充分填充; 较小的收缩性,保证冷却后压印结构不变; 较好的抗刻蚀性,保证压印图形完整转移 |
脱模:
有三种情况脱模会对压印图形造成破坏:
压印材料黏附在印模上
印模图形侧壁表面粗糙,当印模拔出时在印模和压印图形之间形成较大摩擦力
印模浮雕结构的侧壁坡度不合理,当拔出印模时连带将压印材料拔出
希望是正坡度或零坡度边壁,但一般难以获得深宽比高的压印图形
采用双层压印材料涂层可实现高深宽比图形结构的压印
紫外固化纳米压印技术
与热压纳米压印的基本区别:
采用了透明印模
采用可以经紫外固化的液体压印材料,其室温下黏度低
没有固化的有机聚合物可以像未被曝光的负型光刻胶一样通过显影清洗掉
如果衬底是透明的,则用非透明印模也可以实现紫外固化印模
闪光压印:因为光敏剂涂层很薄,只需要极短的紫外光照射即可固化
曝光-压印混合光刻可以同时获得尺寸差异巨大的图形结构
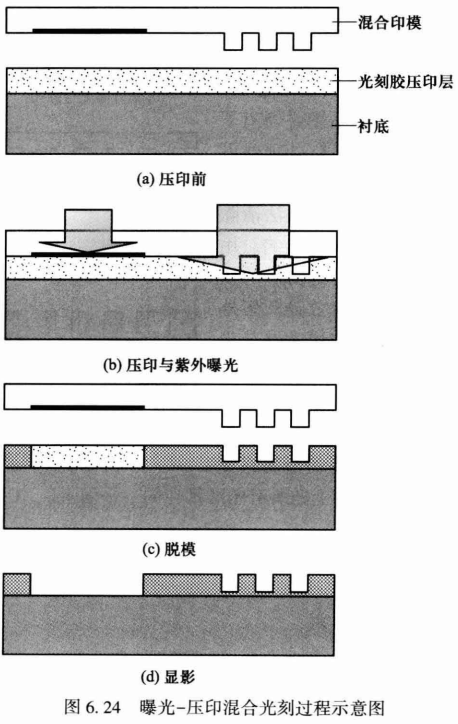
纳米转印技术
也称为反向纳米压印
纳米转印是先将有机聚合物材料涂覆到印模上,待压印材料均匀填充印模浮雕图形表面后,再将印模压到一个平面衬底上,最后移开印模,使印模上的压印结构转移到平面衬底上
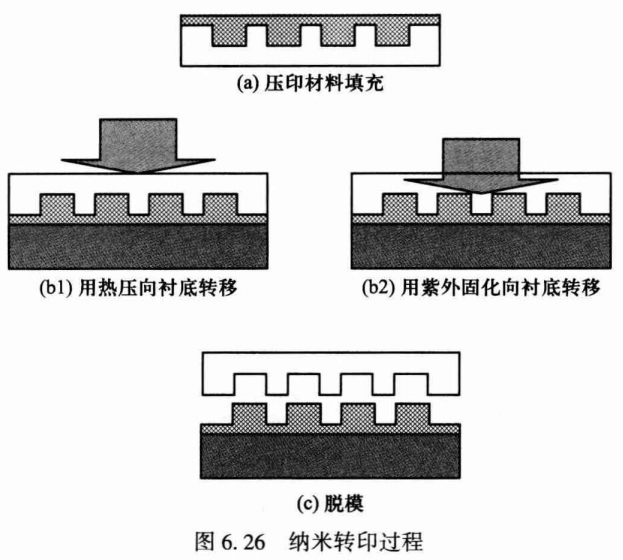
纳米转印成功的关键是衬底材料的表面能大于印模材料的表面能
与纳米压印相比的优点:
- 即使衬底表面已有图形也能进行转印,可加工多层结构
- 由于压印材料是注入而非挤压入印模空腔中,纳米转印较容易实现高深宽比图形结构的制作
课后复习题:
- 纳米压印技术的特点是什么?
- 纳米压印过程包括的主要步骤?
镀膜技术
薄膜生长技术:化学工艺(CVD、电镀等)、物理工艺(PVD)
沉积过程中若沉积粒子来源于化合物的气相分解反应,则称为化学气相沉积(CVD),否则称为物理气相沉淀(PVD)
气相沉积基本过程包括三个步骤:
- 靶材的气化
- 蒸镀材料向所镀制的基片输送
- 蒸镀材料沉积在基片上构成膜层
物理气相沉淀PVD
气相物质的产生:
- 蒸发镀膜:镀料加热蒸发
- 溅射镀膜:用具有一定能量的离子轰击靶材(镀料),从靶材上击出镀料原子
PVD所需实验条件:高真空 (HV);高纯材料;清洁和光滑的衬底表面;提供能量的能源
1标准大气压 = 760mmHg = 760 (Torr)
1Torr=133.3Pa
低真空($10^{-1}$Pa) :机械泵;较高真空($10^{-3}\sim 10^{-4}$Pa):扩散泵;更高真空:分子泵
真空度的影响:对高功函数金属影响相对小;对低功函数金属影响非常大(真空度低会氧化)
蒸发镀膜的缺点:
- 最大缺点是不能产生均匀的台阶覆盖
- 不同材料的蒸气压不同,使得沉积任意精度的合金组分难以实现
热蒸发镀膜 | 电子束(热)蒸发 | |
---|---|---|
原理 | 利用欧姆加热或电磁感应加热材料 | 利用高能聚焦电子束溶解蒸发材料 |
特点 | 无法蒸发难溶材料,蒸发率低,易污染 | 适用于高纯和高熔点物质的蒸发,避免与坩埚材料发生反应 |
注意:高熔点靶材一般不适合使用lift-off工艺,其沉积过程往往需要在高温环境下进行,这会使光刻胶发生软化、分解甚至失效,从而影响图案的精度和lift-off效果。对于高熔点靶材,刻蚀工艺通常是更合适的选择
溅射镀膜的优点:
- 具有淀积并保持复杂合金原组分的能力
- 能够淀积高温熔化和难熔金属
- 能够在直径为200毫米或者更大的硅片上淀积均匀薄膜
- 能够在淀积金属前清除硅片表面沾污和本身的氧化物(被称为原位溅射)
磁控溅射:
附加磁场的优点:
- 限制溅射离子的轨道
- 增加离子在气体中停留的时间
- 增强等离子体和电离过程
- 减少从靶材到衬底路程中的碰撞
- 高磁场附近的产值比较高
磁场的存在将延长电子在等离子体中的运动轨迹, 提高了它参与原子碰撞和电离过程的几率
对比热蒸发/电子束蒸发镀膜和磁控溅射镀膜工作原理差别和成膜特点【课后复习题】
工作原理:
热蒸发/电子束蒸发镀膜 | 磁控溅射镀膜 |
---|---|
通过加热靶材,使其从固态转化为气态,在基底表面凝结沉积薄膜 | 利用惰性气体在靶材表面形成等离子体,在电场作用下轰击靶材表面,溅射出靶材原子,使其沉积在基底上 |
成膜特点:
热蒸发/电子束蒸发镀膜 | 磁控溅射镀膜 | |
---|---|---|
薄膜质量 | 平坦基底上均匀性好,复杂基底上均匀性差 致密性差,可能存在孔隙 |
均匀性、致密性好 对复杂基底形状适应性好 |
薄膜附着力 | 较低 | 较高 |
沉积速率 | 较快 | 较慢 |
适用材料 | 低熔点材料 | 广泛,尤其高熔点材料 |
膜厚控制 | 简单,精度高 | 复杂,精度一般 |
课后复习题:
- 对比热蒸发/电子束蒸发镀膜和磁控溅射镀膜工作原理差别和成膜特点?
薄膜沉积技术
什么是PLD和MBE沉积技术?各自的优缺点是什么?【课后复习题】
PLD脉冲激光沉积(Pulsed Laser Deposition) | MBE分子束外延(Molecular beam epitaxy) | |
---|---|---|
定义 | 通过高能激光束照射靶材表面,使其局部蒸发或激发成等离子体,并使这些蒸发的物质飞向基底的薄膜沉积技术 | 在极高真空下,通过精确控制分子束的流量、能量和方向,将原子层级的材料沉积到基底上的薄膜生长技术 |
优点 | 1. 无污染又易于控制; 2. 靶膜成分接近一致,适合制备具有复杂成分和高熔点的薄膜; 3. 多靶材组件变换灵便,容易制备多层膜及异质结 |
1. 精确的原子层厚度控制; 2. 能生长高质量的单晶薄膜,适用于复杂半导体器件; 3. 可实现原位观察、实时监测; 4. 非热平衡生长,可实现低温生长 |
缺点 | 1. 不易于制备大面积的膜; 2. 薄膜均匀性较差; 3. 仅适用于实验室 |
1. 沉积速率慢; 2. 设备复杂且昂贵 |
课后复习题:
- 什么是PLD和MBE沉积技术?各自的优缺点是什么?
- 金属CVD的特点和优势
原子层沉积ALD
金属CVD的特点和优势: 【课后复习题】
优良的台阶覆盖、通孔无间隙式填充、高深宽比接触、适应性广泛
原子层沉积(ALD, atomic layer deposition)是一种基于有序、表面自限制反应的CVD技术
虽然它与PVD有相似之处,但ALD的特点在于其通过交替引入反应物气体,以实现非常精确的薄膜生长
ALD生长薄膜的基本过程:【课后复习题】
- 准备:真空,各点温度,阀门状态,气压等
- 脉冲通入前驱体1
- 抽气
- 脉冲通入前驱体2
- 抽气
- 回到步骤2,循环
- 结束:关阀门,降温,检查等
为什么ALD可以实现单原子层的薄膜生长?【课后复习题】
主要得益于其表面自限制反应;
在每个ALD循环中,前驱体分子只能在基底表面形成单原子层结构,随后另一种前驱体分子与其反应,继续沉积另一个单原子层
ALD和CVD生长薄膜的过程有什么不同?【课后复习题】
ALD | CVD | |
---|---|---|
前驱体 | 前驱体交替进入反应室; 在工艺温度中不能分解; |
前驱体通常是同时引入的; 通常需要高温来促进反应; |
厚度控制 | 通过反应的循环次数,精确控制 | 通过工艺参数控制,精度较低 |
薄膜质量 | 高均匀性和致密性,缺陷少 | 薄膜质量高,但可能存在微量缺陷 |
沉积速率 | 较慢,每次仅沉积单原子层 | 较高,适合大规模沉积 |
工艺温度 | 温度较低(有利于热敏材料沉积) | 温度较高(通常 500℃ ~ 1000℃) |
如何避免在ALD过程中可能会出现CVD的过程:【课后复习题】
在引入下一种前驱体之前,彻底清除反应室中多余的前驱体和副产物
将反应温度保持在适当范围内,避免高温导致的CVD现象
控制前驱体的流量和暴露时间,防止过量反应
课后复习题:
- ALD生长薄膜的基本过程是什么?为什么ALD可以实现单原子层的薄膜生长?
- ALD和CVD生长薄膜的过程有何不同?如何避免在ALD过程中可能会出现CVD的过程?
化学气相沉淀CVD
CVD的传输和反应过程:
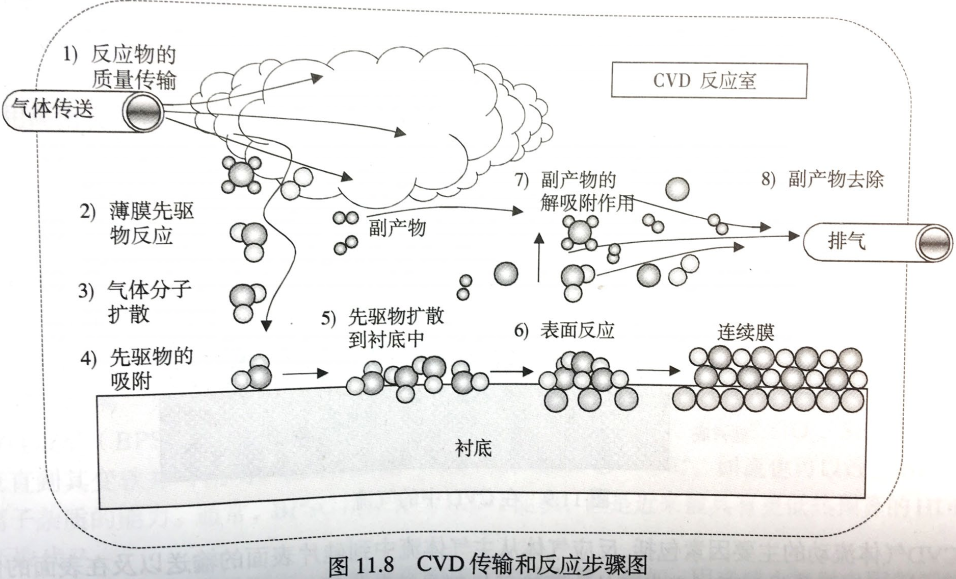
CVD的反应条件:
- 必须达到足够的沉积温度(高温CVD:>900度,中温CVD:700~900度)
- 在沉积温度下,参加反应的各种物质必须有足够的蒸气压
- 参加反应的各种物质必须是气态(也可由液态蒸发或固态升华成气态),而反应的生成物除了所需材料为固态外,其余也必须为气态
- 在沉积温度下,沉积物和基底材料本身的蒸气压要足够低
CVD产物质量的影响因素:
沉积温度:一般来说,温度越高,CVD化学反应速度加快
沉积温度过高,会造成晶粒粗大;沉积温度过低,反应不完全,产生不稳定结构和中间产物
沉积室压强
压强会影响沉积室内热量、质量及动量传输
反应气体分压(配比)
直接影响成核、生长、沉积速率、组织结构和成分
CVD的优缺点:
优点 | 缺点 |
---|---|
薄膜质量高,致密性好; 膜厚均匀,适合大面积沉积; 可沉积多种材料; 沉积速度可以大范围调节 |
前驱体气体具有腐蚀性和毒性; 很难控制多组分的材料沉积; 工艺温度较高,热敏材料受限; |
沉积图像转移
溶脱剥离法lift-off
蒸发和等离子溅射是适用于溶脱剥离法的常用薄膜沉积技术
溶脱剥离法是制作金属薄膜图形的主要方法, 因为许多金属材料都无法或者难以用刻蚀法形成图形
溶脱剥离法的过程:【课后复习题】
- 根据需要去除的涂层材料特性选择合适的溶剂
- 将溶剂均匀涂覆在材料表面,或将材料浸泡于溶剂中,使溶剂与涂层充分接触
- 保持溶剂与涂层接触一定时间,溶解或软化涂层,直至可以剥离
- 用水或其他适当的清洗剂去除材料表面残留的溶剂和涂层,再将材料干燥以恢复其表面状态
成功实现溶脱剥离的关键:【课后复习题】
关键是保证沉积在光刻胶上与沉积在衬底上的金属薄膜不连续
- 沉积金属薄膜厚度远小于光刻胶层厚度
- 薄膜只沿垂直方向沉积
溶脱剥离的局限性:【课后复习题】
- 图形结构的高度受限:沉积的金属膜的厚度必须小于抗蚀剂或者光刻胶厚度的1/3,因此无法获得高深宽比图像;
- 溶剂选择受限:部分材料不易被常规溶剂溶解
- 操作效率较低:较厚或结构复杂的涂层可能需要更长的时间才能溶解
- 表面损伤风险:溶剂的侵蚀作用可能会破坏基材表面或导致表面粗糙度改变
改进方法:改进溶剂配方,改进曝光和光刻工艺,引入保护层
热蒸发镀膜
热蒸发镀膜特点:【课后复习题】
具有较好的方向性,但沉积速率取决于蒸发源与衬底的距离及相对位置
在非垂直于蒸发源的位置,薄膜沉积的方向性会受到影响,进而会影响剥离转移的成功率
可把样品放置于球面支架上,可获得均匀膜厚和改善方向性
溅射镀膜
溅射镀膜特点:【课后复习题】
溅射成膜的质量好,且衬底温升低,在需要高质量薄膜图形情况下多采用溅射沉积,但溅射法沉积的方向性不如热蒸发沉积法
溅射沉积方向性差的主要原因:溅射靶原子在达到样品之前会经历空间气体原子的频繁碰撞散射,导致靶原子沉积的方向性降低,且溅射靶的尺寸要远远大于热蒸发沉积系统的蒸发源尺寸
改善溅射沉积方向性的两项措施:
增加电极间距
增加电极间距后,大角度发射的靶原子沉积到样品表面概率降低,也提高方向性,但缺点是靶材料的利用效率降低
安装准直管
准直管只允许垂直或接近垂直飞行的溅射靶原子达到样品表面,大角度发射的靶原子均落在准直管的侧壁
沉积合金薄膜时,溅射法更优于热蒸发法,因为不同组分的热蒸发温度不同,导致膜的组分可能不同于靶的组分
为什么说热蒸发镀膜和溅射镀膜是适用于溶脱剥离法的薄膜沉积技术【课后复习题】
热蒸发镀膜和溅射镀膜都具备良好的薄膜厚度控制、适中的附着力以及材料多样性,能够形成适合溶脱剥离法的薄膜结构。这些特点使得溶剂能够有效地渗透、溶解或剥离这些薄膜,从而实现高效的溶脱剥离过程。
下切截面(undercut)
光学曝光形成的光刻胶截面一般都是上切(overcut)截面
什么是下切截面?【课后复习题】
下切截面通常是指在材料加工过程中,沿着特定深度或角度对材料的表面进行部分削减或刻蚀,使其在垂直于加工方向的截面上呈现出“下切”或“凹陷”的特征
为什么要下切截面?【课后复习题】
- 如果光刻胶图案的侧壁是垂直的或向上倾斜的,薄膜材料在沉积过程中容易在光刻胶的侧壁上连续覆盖,形成“桥梁”结构
- 下切截面确保了薄膜在光刻胶和基底之间有一个明显的分离区域,提高脱离效率
有什么方法可以实现下切截面?【课后复习题】
多层光刻胶工艺;湿法刻蚀;倾斜曝光:
课后复习题:
- 溶脱剥离法的过程是什么?成功实现溶脱剥离的关键是什么?溶脱剥离法有何局限性,如何解决?
- 比较一下热蒸发镀膜和溅射镀膜的特点。为什么说它们是适用于溶脱剥离法的薄膜沉积技术?
- 什么是下切截面?为什么要下切截面?有什么方法可以实现下切截面?
刻蚀技术
刻蚀技术的重要参数:【课后复习题】
刻蚀速率、刻蚀方向、刻蚀均匀性、抗刻蚀比、精细度
抗刻蚀比:描述刻蚀剂对不同材料刻蚀速率的比值,抗刻蚀比=目标材料的刻蚀速度/掩膜材料的刻蚀速度,高抗刻蚀比好
主要分为湿法刻蚀和干法刻蚀
- 湿法刻蚀:通常为各向同性刻蚀,具有高选择性,图形尺寸可控性差
- 干法刻蚀:单纯的物理刻蚀为各向异性刻蚀,无选择性,图形尺寸可控性高,适于小图形制作,对于离子增强或反应离子刻蚀既包含物理刻蚀也包含化学刻蚀作用
湿法刻蚀
湿法腐蚀包含三个主要步骤:
- 反应物通过扩散方式到达反应表面
- 化学反应在表面发生
- 反应生成物通过扩散离开表面
湿法刻蚀的特点:【课后复习题】
一般为各向同性;高选择性;图形尺寸可控性差;
湿法刻蚀的速度与什么有关?【课后复习题】
刻蚀剂的浓度、刻蚀温度、材料的性质、搅拌速度
课后复习题:
- 考察刻蚀技术的重要参数是什么?
- 湿法刻蚀的特点是什么?
- 湿法刻蚀的速度与什么相关?
干法刻蚀
干法刻蚀技术:广义上指所有不涉及化学腐蚀液体的刻蚀技术,狭义上的干法刻蚀主要指利用等离子体放电产生的物理和化学的刻蚀过程
反应离子刻蚀RIE:
反应离子刻蚀可简单归纳为离子轰击辅助的化学反应过程
需满足两个必要条件:
- 具有离子与化学活性气体的参与
- 刻蚀反应物必须为挥发性物,能够被真空系统及时抽走
反应离子刻蚀的微观过程有哪些:【课后复习题】
物理溅射、离子反应、产生自由基、自由基反应
刻蚀气体的选择:
- 一般硅及其硅化物的刻蚀气体主要以氟化物为主
- III-V族元素化合物材料如GaAs和铝及其化合物的刻蚀气体以氯化物为主
- 某些III-V族元素化合物半导体材料(GaAs、InP)用氢或烷基气体刻蚀更有效
- 选择刻蚀气体时应选择生成物沸腾温度低的气体,以便生成物能及时被抽走,有时需对样品台加温
考察反应离子刻蚀性能的主要技术指标:
- 掩模材料对衬底材料的抗刻蚀比
- 各向异性度
- 刻蚀速率
- 刻蚀均匀性
反应离子刻蚀的工艺参数:
反应气体流量:流速太快将导致反应气体分子在反应室停留时间缩短,或如果流速太低, 被消耗的反应气体得不到及时供给,都会导致刻蚀速率下降;
放电功率:增加放电功率一般会增加刻蚀速度;但是使得离子对处于阴极表面的样品表面的轰击增加,降低掩模的抗刻蚀比,刻蚀速度和抗刻蚀比不可兼得
反应室气压:低气压下离子轰击刻蚀占主导;高气压时化学反应刻蚀占主导地位
被刻蚀样品表面温度:刻蚀速率随温度增加,温度升高的另一个效应是横向刻蚀速率增加,使刻蚀的各向异性度变差,因为化学反应是各项同性的
电极材料:要求阴极材料是化学惰性的,否则阴极本身也会与样品一样被刻蚀
辅助气体:卤素气体中加入少量氧气或氩气会不同程度改进刻蚀效果
如何实现反应离子深刻蚀?【课后复习题】
两个条件:
高刻蚀速度和高抗刻蚀比——电感耦合等离子体刻蚀ICP
通过感应线圈将射频功率从外部耦合进入等离子体发生腔体,等离子体产生区与刻蚀区分开,满足了高刻蚀速度和高抗刻蚀比两个矛盾的要求
极好的各向异性——Bosch工艺
通过交替转换刻蚀气体与钝化气体,在反应离子刻蚀的过程中不断在边壁上沉积抗蚀层或钝化层,从而增加刻蚀的各向异性
在Bosch工艺中由于刻蚀与钝化相互转换,而每一步刻蚀都是各向同性的,因此造成刻蚀边壁表面成波纹状(波纹效应)
反应离子深刻蚀中存在的问题:
负载效应: 局部刻蚀气体的消耗大于供给引起的刻蚀速度下降或分布不均匀的效应
微沟槽效应: 刻蚀过程中边角的刻蚀深度大于中心部分刻蚀深度的现象
缺口效应:刻蚀到绝缘层后不停止,继续沿绝缘层表面横向刻蚀的现象
离子损伤效应:对刻蚀表面的载流子分布和晶体结构造成损伤
对于单晶材料, 离子损伤一般可以通过高温退火工艺消除,但最效的降低离子损伤的办法是降低离子能量
等离子体刻蚀:纯粹的等离子刻蚀主要是化学刻蚀
主要是作为表面干法清洗工艺,各向同性的刻蚀性质使得它被广泛用来清除牺牲层
离子溅射刻蚀:纯粹的物理刻蚀过程,通过惰性气体(通常是氩气)离子的加速撞击,直接将表面原子溅射出去
说明反应离子刻蚀、等离子刻蚀和离子溅射刻蚀的区别 【课后复习题】
属性 | 反应离子刻蚀 | 等离子刻蚀 | 离子溅射刻蚀 |
---|---|---|---|
刻蚀机制 | 物理撞击 + 化学反应 | 化学反应 | 物理撞击 |
方向性 | 各向异性 | 各向同性 | 各向异性 |
刻蚀速度 | 中等 | 较慢 | 较慢 |
刻蚀选择性 | 较好 | 较差 | 差 |
物理损伤 | 中等 | 较少 | 较大 |
侧壁形貌 | 侧壁垂直,适合精细结构 | 侧壁较为圆滑 | 侧壁不定 |
适用材料 | 半导体材料 | 各种材料 | 金属、耐腐蚀材料 |
典型应用 | 微电子器件光刻后处理 | 表面清洁、薄膜去除 | 一般作为薄膜沉积工具 |
课后复习题:
- 反应离子刻蚀的微观过程有哪些?
- 如何实现反应离子深刻蚀?
- 说明反应离子刻蚀、等离子体刻蚀和离子溅射刻蚀的区别?
真空技术
真空:气体分子数量低于大气压状态的空间,但不是完全没有
标准大气压:0度时,760mm 水银柱产生的压强 1atm=1.033$\mathrm {kg/cm^2}$=760 Torr
工业大气压:1am=1$\mathrm {kg/cm^2}$=735.56 Torr
起始压强:真空泵开始工作的允许压强,泵的工作原理决定
有些需要真空下开始工作,因此前级泵是必须的
真空泵的分类:
抽气式 | 吸气式 |
---|---|
旋片式真空泵 扩散泵 涡轮分子泵 分子拖拽泵 |
冷凝泵 离子泵 升华泵 |
常见的几类真空泵的工作原理:【课后复习题】
真空泵类型 | 工作原理 |
---|---|
旋片式机械泵 | 通过偏心转子上的旋片与泵腔壁之间的滑动,形成多个不断变化的密封腔室,逐步吸入气体并压缩排出,从而实现真空抽取,广泛应用于粗真空的产生 |
油扩散泵 | 通过加热液体(通常是油)蒸发形成蒸汽,蒸汽流带动气体分子向排气口移动,实现气体的抽取,蒸汽则被冷凝回泵内,适用于超高真空环境 |
钛升华泵 | 通过加热钛使其直接从固态升华为气态,在升华和沉积过程中与活性气体结合形成稳定化合物(TiO,TiN),达到抽气的目的 |
离子泵 | 电子碰撞气体分子发生电离,离子注入撞击钛阴极,钛阴极发生磁控溅射,在阳极上沉积钛膜,气体分子在钛表面被吸附,然后被掩埋 |
冷凝泵 | 通过将气体分子引导至冷却表面,利用低温使气体凝结为液态或固态,从而实现抽气并维持真空 |
机械类、热传导类、电离真空计的工作原理:【课后复习题】
真空度越高,压力越小
类型 | 工作原理 |
---|---|
机械类真空计 | 通过读取气压对弹性元件的变形量来计算真空度 |
热传导类真空计 | 气体的热传导能力和气压相关,通过监测加热元件的温度变化来计算真空度 |
电离真空计 | 气体分子在高能电子作用下被电离,产生的电流大小与气压成正比,通过测量电流大小来计算真空度 |
课后复习题:
- 常见的几类真空泵的工作原理
- 机械类、热传导类、电离真空计的工作原理
洁净技术
微纳器件的主要污染来源:【课后复习题】
- 空气中的颗粒物
- 人体
- 房间
- 水
- 工艺用化学物质
- 工艺用气体
- 工艺设备
- 静电
什么是RCA衬底清洗方法?【课后复习题】
RCA-1清洗 (标准清洗1,SC-1)
目的: 去除有机污染物和部分颗粒
清洗液组成:$ \mathrm {NH_4 OH-H_2 O_2-H_2 O } $ (1: 1: 5)
反应原理:氨水使颗粒松散脱离表面,而过氧化氢提供氧化能力,分解有机物
RCA-2清洗 (标准清洗2,SC-2)
目的:去除金属离子污染
清洗液组成:$\mathrm{ HCl-H_2 O_2 -H_2 O }$ (1: 1: 6)
反应原理: 盐酸通过络合反应有效去除金属离子,过氧化氢增强氧化能力
清洗流程:
- 硅片预处理(如去除颗粒)
- 进行SC-1清洗,去除有机污染
- 用去离子水冲洗,去除残留SC-1
- HF处理,去除氧化层
- 用去离子水冲洗,去除残留HF
- 进行SC-2清洗,去除金属污染
- 用去离子水冲洗干净并干燥
课后复习题:
微纳器件的污染来源有哪些?
什么是RCA衬底清洗方法?
电学测量
电学测量的两个目的:
- 表征纳米材料和器件的电学性能
- 探索新的物理现象和知识
重要概念:在导体中,低温低偏压下,只有能量接近费米能量的电子对电导有贡献
常用的电学测量三种方式
- 半导体参数分析仪
- 基于数据采集卡的测量系统
- 基于GPIB的测量系统
在测量弱电流和小电压时,哪些影响因素会带来测量误差?【课后复习题】
热噪声(Johnson噪声);电磁干扰(EMI);地回路;接触电阻和引线电阻
在测量小电阻时如何避免引线电阻的影响?【课后复习题】
四端法(Kelvin连接)
两根导线用于提供测量电流,另两根导线用于测量电阻两端的电压
由于测量电压的导线没有电流流过,因此引线的电阻不会影响测量结果。
校准和补偿:在测量前,通过短路测量法测量引线的总电阻,将引线电阻值从测量结果中减去
温度控制:引线电阻随温度变化,因此控制测量环境的温度稳定性可以减少测量误差
课后复习题:
- 在测量弱电流和小电压时,哪些影响因素会带来测量误差?
- 在测量小电阻时如何避免引线电阻的影响?
膜厚度测量
椭偏仪的工作原理:【课后复习题】
椭偏仪通过分析光的偏振状态变化来测量材料的光学性质,其核心原理是利用光学偏振和菲涅耳公式,主要测量参数是$ \Psi $ (振幅比变化)和$ \Delta $ (相位差变化)
1 | 光源 --> 偏振器 --> 入射偏振光 --> 样品 --> 反射光 --> 分析器 --> 探测器 --> 数据处理 |
椭偏法测量能够获取哪些材料信息?
薄膜厚度d、折射率n、消光系数k
课后复习题:
- 椭偏仪的工作原理是什么? 椭偏法测量能够获取哪些材料信息?
光学测量
为什么要用光学检测?
高精度、非接触、无损检,灵敏度高
光散射的能量变化与其分类:
散射名称 | 能量改变范围 | 散射性质 |
---|---|---|
瑞利散射 | $<10 ^{-5} \mathrm{cm^{-1}} $ | 弹性 |
布里渊散射 | $10^{-5}\sim 1\mathrm{cm^{-1}} $ | 非弹性 |
拉曼散射 | $>1 \mathrm{cm^{-1}}$ | 非弹性 |
光散射研究中,能量通常以波数 $ \tilde \nu $ (波长的倒数) 表示,单位为 $ \color{red} \mathrm { cm^ { -1 } } =0.000124 eV $
拉曼位移表示的是波数变化
$$
E=h\nu=hc\tilde \nu
$$
为什么常用斯托克斯线Stokes line?
斯托克斯散射比反斯托克斯散射的信号强度通常更高
斯托克斯信号在低频端,受热噪声影响较小,信噪比更高
斯托克斯线和反斯托克斯线关于激光频率对称,测量斯托克斯线已足以获取完整的振动信息
拉曼光谱测量的原理:【课后复习题】
拉曼光谱基于拉曼散射效应,当入射光照射到样品表面,大部分光子发生弹性散射(瑞利散射),少部分光子与样品分子的振动能级发生相互作用,发生非弹性散射(拉曼散射),通过测量这些频移,可以获得分子的振动信息
拉曼光谱的特征:【课后复习题】
(1)改变入射光频率,散射光相对入射光的拉曼频移总是不变;
(2)斯托克斯和反斯托克斯频移的绝对值相等;
(3)谱峰的形状和强度取决于分子的类型和浓度,每个峰像指纹一样独特;
(4)激发光波长影响光谱质量,短波长激光可能导致样品荧光干扰,较长波长激光可能会提供更清晰的拉曼信号;
荧光光谱测量的原理:【课后复习题】
使用紫外光或可见光等激发光源照射样品,样品吸收光子后,电子跃迁至激发态,当这些激发态电子返回基态时,会以光子的形式释放能量,产生荧光。通过光谱仪对发射光进行分光分析,可以获取样品结构、浓度、环境等信息
阴极荧光光谱(CL)测量的原理:【课后复习题】
将高能电子束聚焦并照射到样品表面,激发材料中电子跃迁至激发态,当这些激发态电子返回基态时,会以光子的形式释放能量,产生荧光。通过光谱仪对发射光进行分光分析,从而获取材料的电子结构、缺陷和杂质信息
二者的区别:
荧光光谱 | 阴极荧光光谱 | |
---|---|---|
激发源 | 光子(紫外光、可见光) | 电子束 |
样品影响 | 无损伤,可以多次测量 | 可能对样品表面造成影响 |
空间分辨率 | 受限于光学衍射,通常在 $ \mu m $ 级别 | 作为扫描电子显微镜的附件,可以实现 $nm$ 级别 |
样品要求 | 常用于液体、气体、固体样品 | 通常为固体,最好导电 |
应用场景 | 化学、生命科学 分析分子或离子浓度、生物标记 |
材料科学、半导体研究 |
课后复习题:
- Raman光谱的原理和特征是什么?
- 荧光光谱, 阴极荧光光谱测量方法的原理和应用特点